Promotion of Social and Environmental Standards in the Industry (PSES)
Project description
Title: Promotion of Social and Environmental Standards in the Industry (PSES)
Commissioned by: German Federal Ministry for Economic Cooperation and Development (BMZ)
Country: Bangladesh
Lead executing agency: Ministry of Commerce, Government of the People's Republic of Bangladesh
Overall term: 2017 to 2020
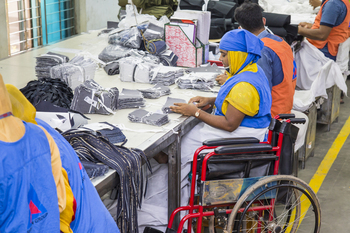
Context
The fashion industry is booming: the design comes from Europe, the cotton from Africa or America, the production of fabric takes place in China. The fabric is then brought to Bangladesh, where the garment industry produces T-shirts and other textiles out of it, which consumers purchase in the shops in Europe.
As a major player in the industry, Bangladesh is at the centre of the globalisation of the textile sector and, therefore, receives attention worldwide. The textile and garment industry is the second largest in the world and topped only by China. It has an export volume of USD 28.15 billion for the 2016-2017 fiscal year. Four million people, most of them women, are employed in the approximately 4,500 textile and garment factories.
It is the stated goal of the Government of Bangladesh to achieve further growth. Therefore, they are planning to increase the revenues of garment exports to USD 50 billion by 2021. However, the time of rapid growth at all costs is over. Growing social pressure from consumers and, consequently, buyers in Europe and the US, is a major factor in initiating a change of thinking within the industry.
While there are clear statutory requirements for compliance with social and environmental standards, many businesses are still not equipped to fulfil them. Government actors need expertise and personnel to enforce the legislation, while factories and tanneries require knowledge and qualified staff familiar with social and environmental norms.
Objective
The project “Promotion of Social and Environmental Standards in the Industry (PSES)” is supporting the government and actors of the private sector as well as civil society to pursue a course of sustainable economic growth in the textile, garment and leather industries in Bangladesh.
It is essential that:
- Government representatives are equipped to enforce the legislations
- Factories and tanneries are willing and able to improve environmental and social standards and can increase their productivity at the same time
- Workers know their rights and assert them in the factories
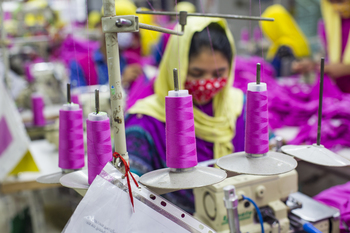
Approach
The project is supporting Bangladesh’s garment, textile and leather sectors to increase compliance with national labour and environmental laws and international standards to fulfil the commitment towards an inclusive workforce. PSES is primarily concerned with legislation and standards for safeguarding the rights of workers, including provisions for the inclusion of persons with disabilities. It builds on the work of its predecessor projects, which ran from September 2009 to June 2017.
The project experts work together with all stakeholder groups, including ministries, employers’ associations, factories, international buyers, non-governmental organisations and trade unions. It assists government representatives and factory managers to improve working conditions and to implement environmental standards. At the same time, the project supports workers to know their rights and responsibilities and helps them to assert these rights and responsibilities in the factories. Through its “Inclusive Job Centre” the project supports the integration of persons with disabilities into the sectors’ workforce.
The project helps to achieve sustainable development in the ready-made garments (RMG), textile and leather sectors, helping the Government achieve its Vision 2021, aiming at export revenue of USD 50 billion by 2021 in these sectors. As a partner to business, government and civil society, PSES contributes to strengthening the systemic competitiveness of Bangladesh's textile and leather industry in its sustainable economic, social and environmental dimensions.
GFA Consulting Group supports the implementation of the project, particularly in the area of strategy development and road map
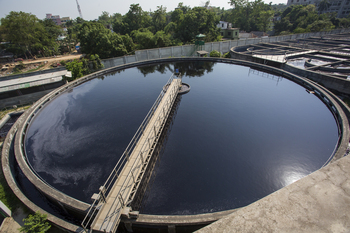
Results
from January 2010 to June 2019:
- More than 1,000 partner factories have delivered measurable improvements to their working conditions through PSES’ factory improvement programme in the RMG and leather sectors
- More than 270,000 workers, mostly female, have been provided information of their rights as well as responsibilities through women’s cafés, for the improvement of social dialogue and industrial relations in the RMG and leather sectors
- More than 10,000 disputes between workers and management in the garment sector have been resolved amicably through women’s cafes
- A mini fire brigade has been piloted, showing the effectiveness of professional fire response teams and resources being located directly in industrial areas, reducing the risks to workers
- More than 300 persons with disabilities received support in finding a suitable job in a factory
- More than 2100 persons were trained on vocational qualifications to obtain employment in the garment and textile industries. Among them 286 were persons with disabilities.
- More than 300 factories have improved their environmental standards in areas such as solid waste and wastewater management, electrical safety, water reduction, chemical management and energy consumption
- National standards and guidelines for sludge management have been developed jointly with the Department of Environment (DoE)
- The International University of Business Agriculture and Technology (IUBAT) now offers a certification course on wastewater management using toolkits, training modules and training provided by GIZ