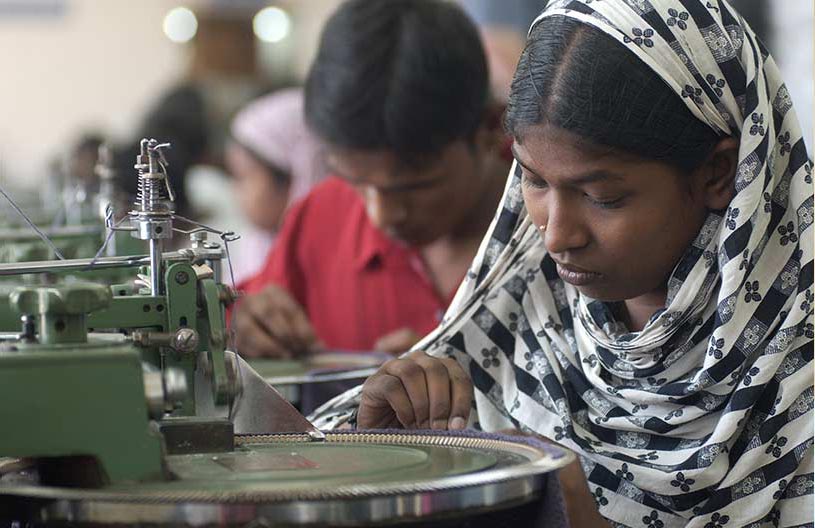
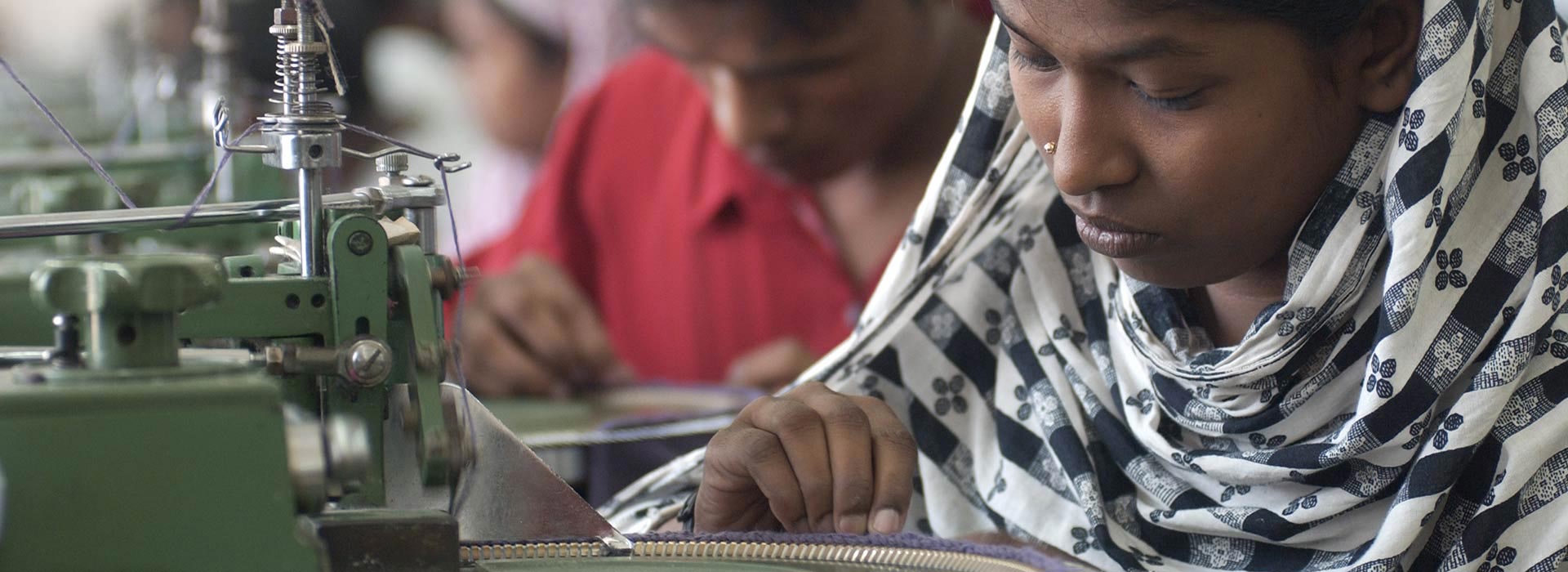
Economic development and employment: Bangladesh: producing socially-conscious and eco-friendly clothing
Bangladesh’s textile and clothing industry has not only grown rapidly in recent decades, it has also developed further in terms of complying with social and environmental standards.
Bangladesh is the world’s second largest exporter of clothing and textiles after China, making it one of the key players in the global textile industry. Although the situation of workers has increasingly improved in recent years, the industry still has a lot of room for improvement.
More than 4.5 million people in Bangladesh work in the textile industry, and the vast majority of them are women. The government has declared its aim to grow the industry even further and increase annual exports of textiles and clothing to USD 50 billion by 2021, which is almost double the figure for 2016. Legislation and enforcement has developed significantly in many areas since the Rana Plaza accident. These include, for example, trade union representation, minimum wages and job security. Nevertheless, many textile factories have still not reached the standards set by the International Labour Organization (ILO). For example, a key challenge is the inadequate protection of employees from work-related illnesses or accidents. The industry’s continuing growth is also impacting the environment: a particular feature of textile production (e.g. dyeing and printing) is its very high consumption of water, chemicals and energy. In addition, rivers, waters and soils are polluted by the improper disposal of untreated waste water and residues. These pollutants have considerable consequences for the surrounding population and the immediate ecosystems.
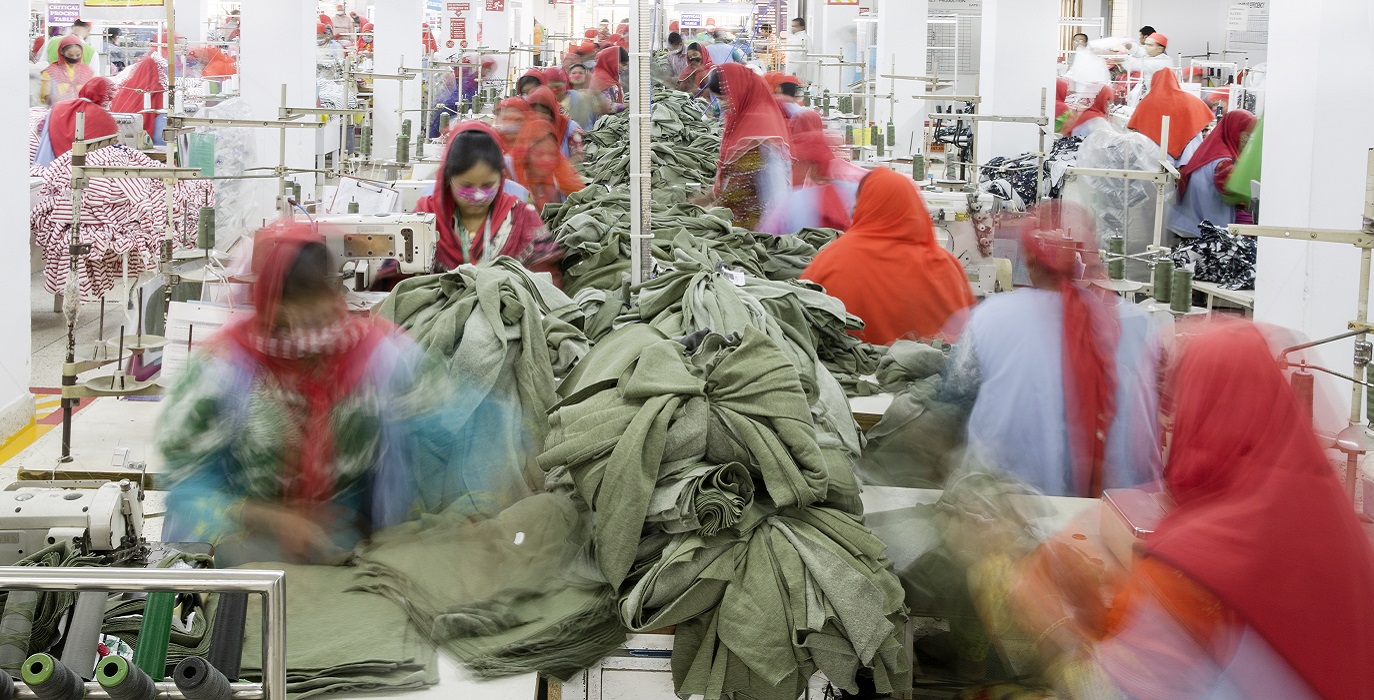
Knowledge – the key to better standards
The Deutsche Gesellschaft für Internationale Zusammenarbeit (GIZ) GmbH has been helping improve social and environmental standards in Bangladesh’s textile industry since 2005. On behalf of the German Federal Ministry for Economic Cooperation and Development (BMZ) and with funding from the European Union (EU), GIZ has trained managers and staff on issues relating to fair pay, fire safety and the safe handling of chemicals. As part of a factory improvement programme, it has helped business associations carry out over 5,000 inspections in more than 1,800 factories. 1,600 of the factories inspected have demonstrably improved their compliance with social standards. Moreover, GIZ is also collaborating closely with the ILO and the Dutch Embassy on introducing a statutory accident insurance scheme. The issue of safety is also being addressed at factory level: for example, risk assessments have been carried out, including training to improve workplace safety, in 80 factories with a total of more than 180,000 employees. Because the textile industry in Bangladesh also provides work for people with disabilities, a special advisory centre for these workers was set up. More than 1,000 people have already benefited from its services.
In addition, GIZ has provided training for 70 experts who advise factories and staff on issues relating to environmental protection. Three hundred businesses have been able to significantly improve their environmental standards after receiving such advice – for example, by ensuring proper wastewater management and reducing energy consumption. With GIZ’s support, there are also new solutions for toxic sewage sludge: based on a new guideline issued by the environmental protection agency, the sewage sludge is disposed of cleanly and undergoes further treatment as part of a new business model for cement production. In order to contribute to long-term rethinking in the industry and to mainstream fair and sustainable production patterns in the industry, German and Bangladeshi universities are also jointly examining the curricula for training programmes in the textile sector.
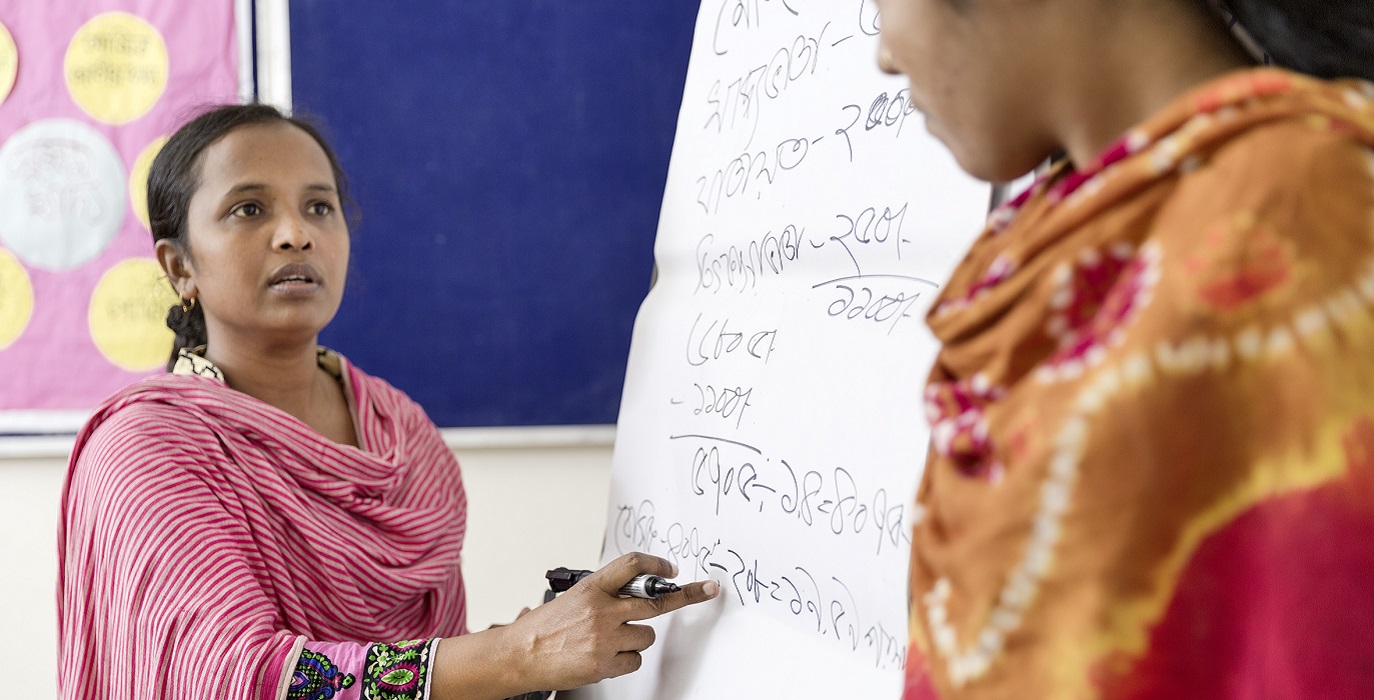
Women’s cafés support female workers
As women account for the majority of workers in the textile industry in Bangladesh, the project has set up around 20 women’s cafés where female workers can meet and exchange views with one another. More than 270,000 women have learned about workers’ rights through training courses and theatrical performances featuring games, posters and films.
The women’s cafés also offer legal advice to users. For example, seamstress Noor Nahar only found out at one of the women’s cafés what minimum wage she was actually entitled to – and was dismissed when she asked to be paid this wage. With the help of the legal advisors in the women’s café, Nahar successfully fought to keep her job. Not only was she reinstated with a better wage – the minimum wage was then also introduced for all the other female workers. Noor Nahar is now one of more than 20,000 women who advise their female colleagues on their rights and the minimum wage levels that are in force.
From Africa to Asia – aiming to make standards universal
Many different parties need to be involved if standards are to be successfully put in place throughout the entire supply chain in clothing production. In Bangladesh GIZ is working with representatives from the state, the private sector and civil society to ensure that all actors take responsibility for shaping the desired economic growth in a sustainable way.
Building on the lessons learned in Bangladesh, the federal enterprise is also working in Ethiopia, Cambodia, Myanmar, Pakistan and Viet Nam. China is also on board as a strategic partner. As an investor, China plays a key role in implementing sustainability standards, especially in the emerging clothing industries in Cambodia and Myanmar.
Last update: March 2020